Chemical process pumps are an essential component of many industrial applications, including chemical processing, oil and gas refining, and pharmaceutical manufacturing. These pumps are designed to handle corrosive, abrasive, and hazardous fluids that are used in these industries. In this article, we will discuss the importance of chemical process pumps and their features that make them suitable for these applications.
Corrosion Resistance
One of the main features of chemical process pumps is their ability to resist corrosion. Chemical fluids can be highly corrosive and can damage conventional pumps made of steel or iron. However, chemical process pumps are made of materials such as stainless steel, titanium, and plastic, which are resistant to corrosion. This makes them suitable for handling corrosive chemicals without causing damage to the pump or contamination of the fluid.
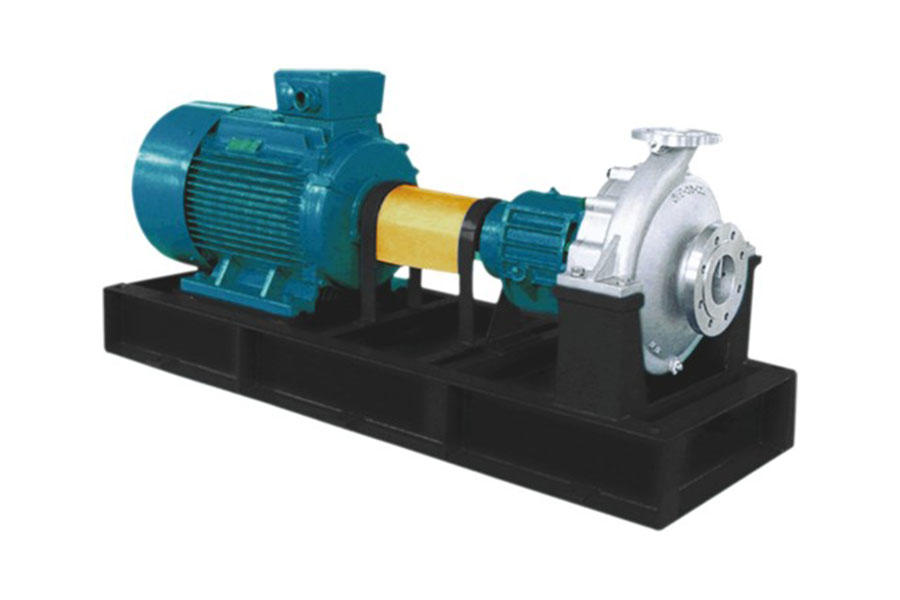
Durability
Chemical process pumps are designed to be durable and long-lasting. They are constructed with heavy-duty materials and components to withstand the demands of continuous operation in harsh environments. They also have features such as reinforced shafts and bearings, which increase their reliability and reduce maintenance requirements.
Sealless Design
Chemical process pumps have a sealless design, which eliminates the need for mechanical seals. Mechanical seals can wear out and leak, causing fluid contamination and pump failure. Sealless pumps have a magnetic drive, which uses a magnetic coupling to transfer power from the motor to the impeller. This design prevents leaks and ensures the integrity of the fluid being pumped.
Wide Range of Flows and Pressures
Chemical process pumps are available in a wide range of flow rates and pressures to suit different industrial applications. They can handle fluids with varying viscosities, temperatures, and densities, making them suitable for a variety of processes. They can also be customized to meet specific flow and pressure requirements.
Energy Efficiency
Chemical process pumps are designed to be energy-efficient, which can reduce operating costs and environmental impact. They have features such as variable speed drives and impeller designs that optimize performance and energy consumption based on demand. This improves efficiency and reduces energy waste.
In conclusion, chemical process pumps are an essential component of many industrial applications. Their ability to resist corrosion, durability, sealless design, wide range of flows and pressures, and energy efficiency make them suitable for handling corrosive, abrasive, and hazardous fluids. With the right chemical process pump, industries can ensure the integrity of their processes while minimizing environmental impact and operating costs.