Choosing a multi-stage chemical process pump for a factory requires careful consideration of various factors to ensure compatibility, reliability, and efficiency. Here are some key steps to guide you in selecting a suitable multi-stage chemical process pump:
Understand Process Requirements: Begin by understanding the specific requirements of your chemical process. Determine the flow rate, pressure, temperature, and the type of fluid being handled. Consider factors such as the nature of the chemicals, their corrosiveness, viscosity, and the presence of solids or abrasives. This information will help you identify the necessary pump specifications.
Chemical Compatibility: Assess the compatibility of the pump materials with the chemicals being pumped. Ensure that the materials used in the pump construction are resistant to corrosion or chemical attack. Consider the chemical resistance of the pump casing, impellers, seals, and other wetted parts. Consult chemical compatibility charts or seek guidance from pump manufacturers to select suitable materials for your application.
Performance Requirements: Determine the desired performance characteristics of the pump. Consider factors such as the required flow rate, head pressure, and efficiency. Multi-stage pumps are capable of generating higher pressures by using multiple impellers, making them suitable for applications that require higher head pressures. Ensure that the selected pump can meet the specific performance requirements of your factory's chemical process.
Reliability and Maintenance: Assess the reliability and ease of maintenance of the pump. Look for pumps from reputable manufacturers known for producing reliable and durable equipment. Consider factors such as the availability of spare parts, the ease of access for maintenance and repairs, and the manufacturer's support services. A pump with a robust design and easy maintenance procedures will minimize downtime and ensure the smooth operation of your factory.
Safety Considerations: Chemical processes often involve hazardous materials, so safety is paramount. Select a pump with safety features such as leak detection, overpressure protection, and temperature monitoring. Ensure that the pump meets safety standards and regulations applicable to your industry. Consult with safety experts or professionals to identify specific safety requirements for your chemical process.
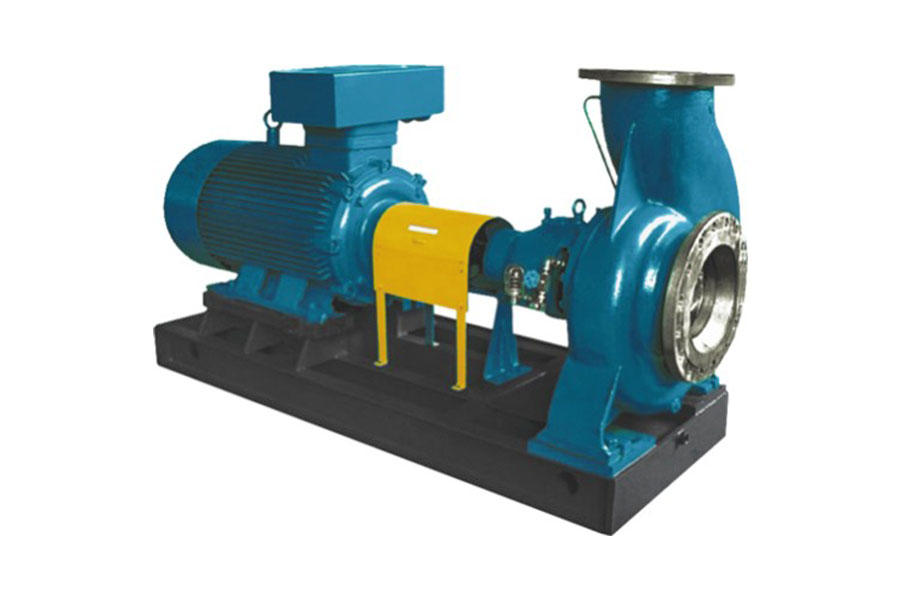
Efficiency and Energy Consumption: Energy efficiency is crucial to minimize operational costs and environmental impact. Look for pumps with high hydraulic efficiency, as well as energy-efficient motors. Consider pumps that meet or exceed industry standards for efficiency, such as those certified by organizations like the Hydraulic Institute (HI). Opt for variable speed drives or controls if the process demands varying flow rates, as they can optimize energy consumption.
Noise and Vibration: Evaluate the noise and vibration levels generated by the pump. Excessive noise or vibration can be detrimental to the work environment and may indicate potential issues with the pump's operation. Look for pumps with low noise and vibration levels, especially if the pump will be installed in close proximity to workers or sensitive equipment.
Compliance and Certifications: Ensure that the selected pump complies with relevant industry standards and regulations, such as ISO, ANSI, or API standards. Look for pumps that are certified for specific applications, such as those approved for handling hazardous or flammable substances. Compliance with standards ensures the pump's suitability, quality, and reliability.
Cost Considerations: Consider the total cost of ownership rather than just the initial purchase cost. Evaluate the pump's lifecycle costs, including installation, maintenance, energy consumption, and potential repairs. A higher quality and more efficient pump may have a higher upfront cost but can result in long-term savings through improved reliability and reduced energy consumption.